Maintaining Quality from Afar: How Faceport Enables Remote Manufacturing Inspections

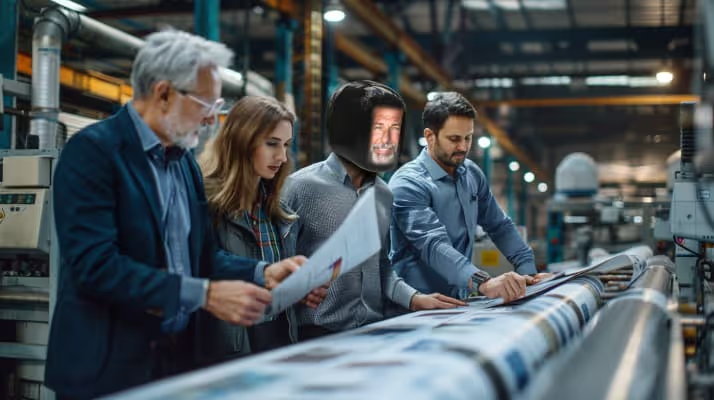
Mark Jensen, an experienced supply chain manager based in San Francisco, had long-standing relationships with his manufacturing partners, ensuring quality and efficiency across operations. Recently, his company was preparing to launch a new product line, which required close oversight of production at a facility in Indianapolis. However, with tight schedules and limited travel options, visiting the plant in person wasn’t feasible.
Rather than delay the inspection, Mark used Faceport’s telepresence technology to participate in the process remotely. From his office in San Francisco, he connected through Faceport, which allowed him to virtually join the team at the Indianapolis facility. The Faceport Helmet, worn by the plant manager, enabled Mark to inspect every stage of the manufacturing process as if he were walking the factory floor himself.
“Let’s take a closer look at that new assembly line,” Mark said, directing the team as they reviewed key production details. He examined the quality of the components and ensured that everything met the company’s high standards. His presence, though virtual, allowed him to ask questions, provide feedback, and address any concerns in real-time.
For Mark, this virtual visit was more than just a convenience—it allowed him to stay on top of critical operations without sacrificing the thoroughness required for quality assurance. “I need to be confident that our processes are efficient and up to spec, and Faceport lets me do that without being on-site,” he reflected.
The team at the manufacturing facility appreciated the ease with which they could collaborate with Mark. “It felt like he was here, offering guidance and expertise just as if we were walking the floor together,” the plant manager noted.
Faceport is designed to be a valuable tool for professionals like Mark, providing a way to maintain hands-on involvement in essential operations across distances, ensuring both quality and timely delivery.