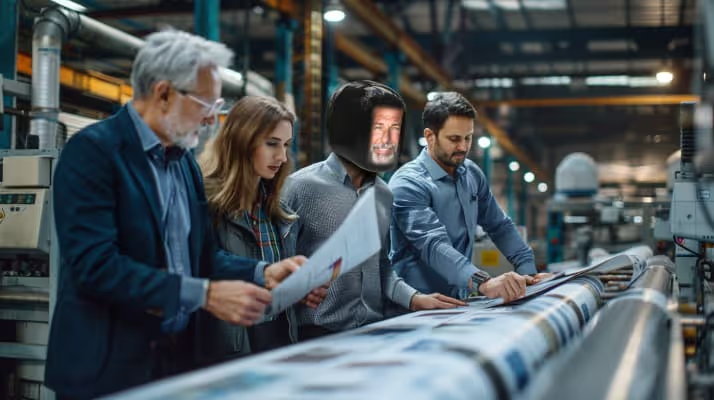
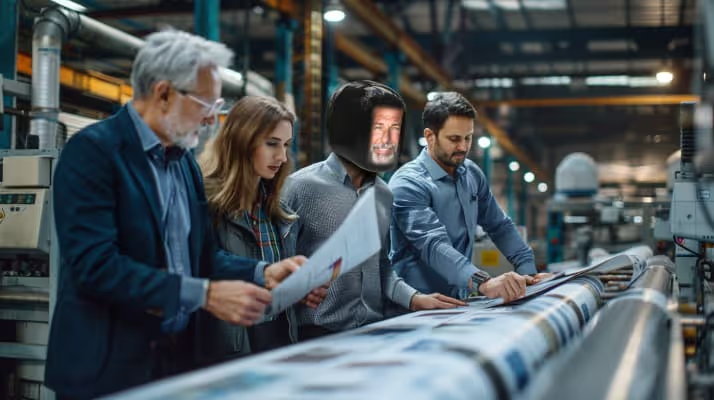
SOLUTIONS
Manufacturing
Faceport, our innovative telepresence platform, transforms the manufacturing industry by enabling real-time, face-to-face interactions through a helmet that displays a remote person's face. This cutting-edge technology enhances communication, improves efficiency, and ensures seamless operations across various manufacturing activities.